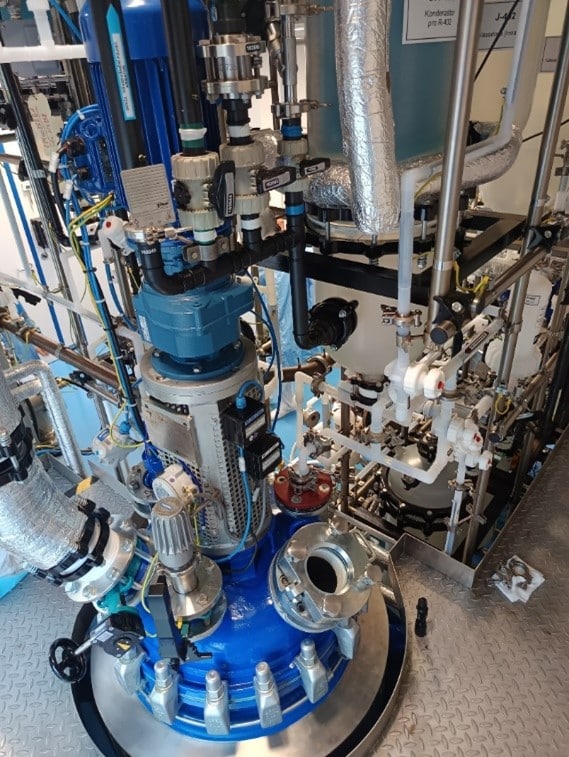
The new production lines D1 and D2 were launched for the first time in May 2024. The first batch of 11 kg of API was produced in the following weeks, and the tremendous efforts of the many people involved in planning the entire production line have finally paid off. Since the production line was launched, all equipment has been continuously utilized.
For more information about this production line, we interviewed our Process Chemistry Specialist, Michal Beneš.
Michal, what was the reason for building the new production lines in Prague?
The main reason for building the new production lines was to adapt to the manufacturing of larger batches of API, with the D1 production line handling up to 5 kg and the D2 production line up to 15 kg. Additionally, the aim was to increase the overall production capacity of the Prague site
What were these production lines planned to be designated for?
The D1 and D2 production lines essentially replicate the C production line, which has been operating in Prague for many years. The primary difference is the volume of the reactors used for API production. Production line D2 now features four new enamel reactors with capacities of 100 and 160 L, while production line D1 is equipped with two 63 L reactors. All reactors are capable of operating within a temperature range of −40 to 140 °C.
What process operations can be performed on these new production lines?
The new production lines support a variety of process operations, including extraction, filtration to remove contaminants, distillation (under vacuum or atmospheric pressure), crystallization, and drying. These operations offer flexibility in producing a range of chemicals and APIs in varying volumes and qualities.
Can you tell us about the optimization and modern technologies used in the construction of these production lines?
A major advantage of these production lines is their location in a cleanroom environment, maintaining cleanliness class D under ISO 8 standards. This setup minimizes worker handling of APIs, reducing the influence of external factors on product quality. Employees and materials access the production line through specialized airlocks, ensuring hygiene standards and maintaining aseptic conditions for materials entering the area.
One key piece of equipment is the filter dryer, which enables filtering, drying, and packing of intermediates and APIs within a closed system.
The production lines are fully controlled and monitored by a computer system equipped with numerous safety features. An automated control panel tracks all production conditions and supports systems. Each device on the production line features multiple sensors to monitor substance concentrations during production. If any limits are exceeded, the sensors immediately alert the operators, ensuring both safety and product quality.
Who are the personnel working on these production lines?
The personnel consist of highly qualified individuals trained to operate the new production lines. Several operators are always present to ensure compliance with all safety regulations and to oversee smooth and efficient production processes.
In conclusion, the new production lines represent a significant advancement for our company, underscoring our commitment to innovation, efficiency, and quality. With state-of-the-art technology, stringent safety measures, and a team of highly skilled personnel, this facility not only enhances our manufacturing capabilities but also reinforces our dedication to meeting the highest industry standards.
As we move forward, these production lines will play a pivotal role in driving our growth and delivering superior products to our customers. We are excited about the opportunities they bring and look forward to their positive impact on our operations and the industry as a whole.